Machining
CapabilitieS
Our manufacturing facility has a diverse range of CNC machines operating on 3 to 5 axes. This means we can handle the machining of small parts and parts up to 1200mm long.
With over 20 years of experience in CAD/CAM, machining, and the development and implementation of manufacturing processes, we ensure that our products are not only cost-efficient but also maintain proper functionality. We possess exceptional proficiency in planning, designing, setting up, improvising, and optimizing manufacturing processes. Our expertise in using cost-effective methods to reduce the impact of production results in delivering high-quality products.
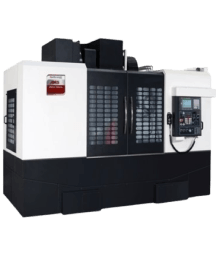
3 AXIS
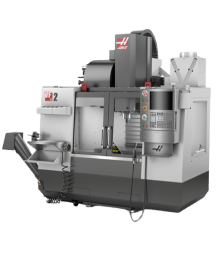
4 AXIS
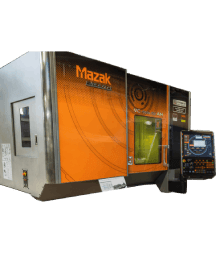
5 AXIS
A quick view at
our products
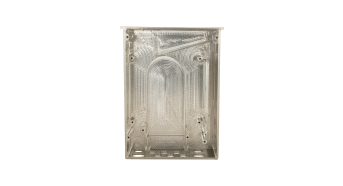
ION CASE 2 – 3
Material: AL 6061 T6
Sur Finish: Electroless Nickel
gold plating
Application: Aerospace
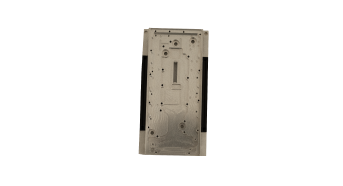
DTRM RX Housing
Material: AL 6061 T6
Sur Finish: Electroless Nickel
gold plating
Application: Aerospace
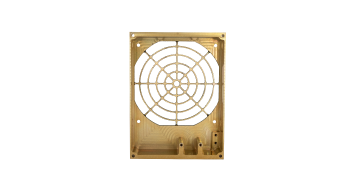
FAN 119X119 BOX
Material: AL 6061 T6
Sur Finish: Electroless Nickel
gold plating
Application: Aerospace
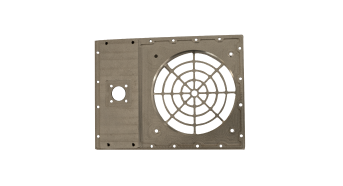
FAN BASE PANNEL
Material: AL 6061 T6
Sur Finish: Electroless Nickel
gold plating
Application: Aerospace
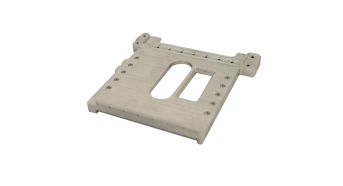
MIDDLE PLATE
Material: AL 6061 T6
Sur Finish: Electroless Nickel
gold plating
Application: Aerospace
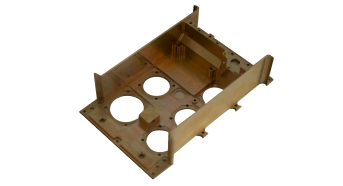
Front Panel Plate
Material: AL 6061 T6
Sur Finish: Electroless Nickel
gold plating
Application: Aerospace
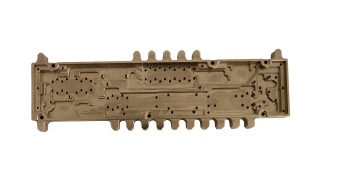
FEDM BLOCK
Material: AL 6061 T6
Sur Finish: Electroless Nickel
gold plating
Application: Aerospace
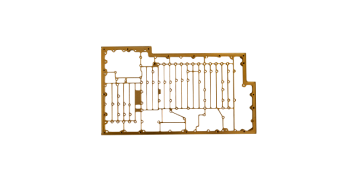
REEHIVE
Material: AL 6061 T6
Sur Finish: Electroless Nickel gold plating
Application: Aerospace
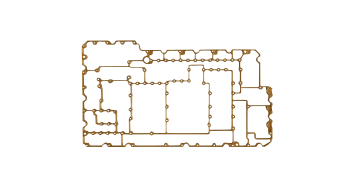
20-40 B FRAME
Material: AL 6061 T6
Sur Finish: Electroless Nickel
gold plating
Application: Aerospace
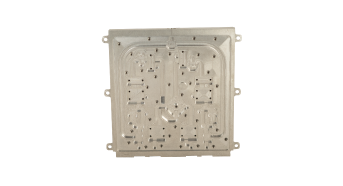
SUPI Body Machining
Material: AL 6061 T6
Sur Finish: Electroless Nickel
Silver plating
Application: Aerospace
our process
Manufacturing
At APSIS AEROCOM LTD. We specialise in providing top-notch machining services for the Aerospace and Healthcare industries. With years of experience and cutting-edge technology, we offer a seamless process that begins with raw material purchase and extends all the way to surface treatment and ready-to-use integration. We will walk you through each step of our meticulous process, highlighting the expertise and attention to detail we bring to every Aerospace and Healthcare component.
Step 1: Raw Material Purchase: To ensure the highest quality standards for our aerospace components, we prioritise a meticulous process that begins with the careful selection and purchase of raw materials. We collaborate with trusted suppliers who adhere to stringent industry specifications and share our commitment to excellence. Our team of experts conducts a thorough analysis of material properties, including strength, weight, and chemical composition, according to customer specifications. By sourcing the finest materials that meet the customer’s requirements,
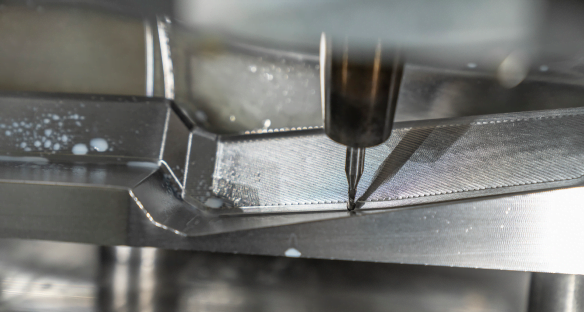
Step 2: Process Engineering: Once the raw materials are procured, our experienced design and engineering team develops detailed plans and specifications for each aerospace component. We utilise state-of-the-art CAD and CAM software to create precise planning and validation processes. Our team collaborates closely with clients to incorporate their specific requirements and optimise the process for manufacturing efficiency and performance.
Step 4: Inspection: To meet the customer’s specifications and ensure the functionality of our aerospace and healthcare components, we conduct thorough inspections at every stage of the machining process. Our dedicated quality assurance team utilises advanced metrology equipment to verify dimensions, perform surface analysis, and conduct non-destructive testing. These rigorous tests ensure that each component meets or exceeds the required specifications, guaranteeing optimum performance and product safety.
Step 5: Surface Treatment: Surface treatment is a critical phase in aerospace component machining as it significantly enhances durability, corrosion resistance, and overall performance. To achieve the highest quality standards, we collaborate with customer-approved surface treatment suppliers who specialise in various advanced methods such as anodizing, plating, painting, and coatings. These treatments are carefully chosen to protect the components from harsh environmental conditions and to ensure optimal functionality in aerospace and healthcare applications, meeting the customer’s specifications. Our team of expert technicians diligently oversees the process, ensuring consistent quality and uniformity across all components.
Step 6: Delivery: Once the components have undergone machining and surface treatment, they undergo meticulous pre-dispatch inspection to ensure their quality and adherence to specifications. After the inspection, the components are securely packaged in preparation for delivery to our clients. We take great care in packaging the components to ensure their protection during transit. Our commitment to meeting deadlines and exceeding expectations ensures that the components are delivered on time and in optimal condition to our valued clients.
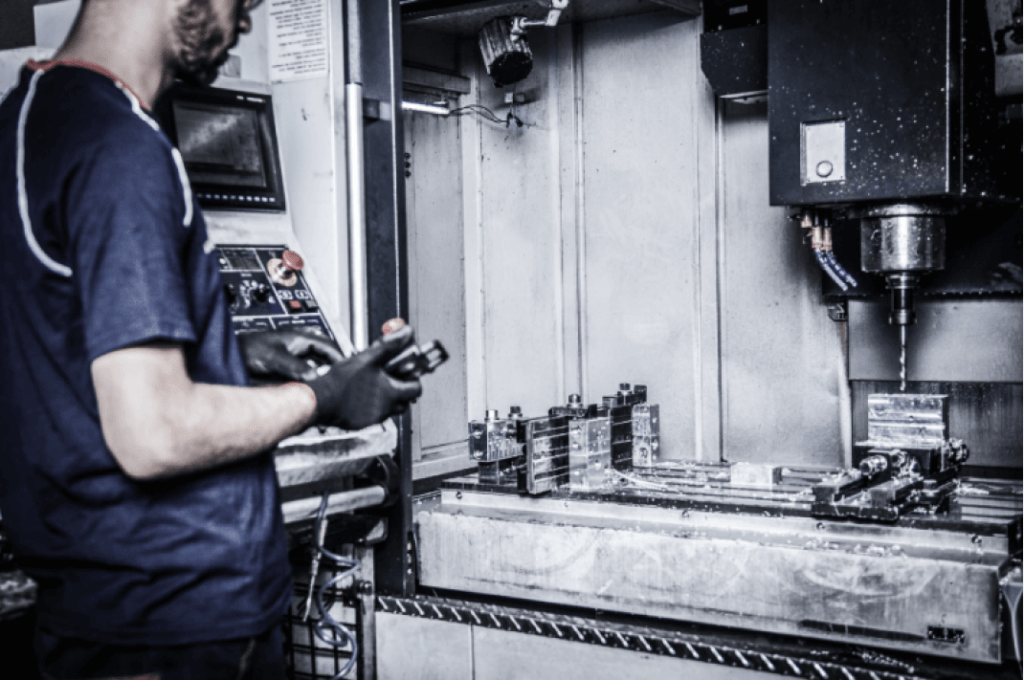
Quality Control
At Apsis, our team of dedicated Quality Heads, Engineers, and Inspectors utilize state-of-the-art machinery to compare our products against acceptance criteria and uphold exceptional quality standards. We once again conduct the First Article Inspection (FAI) in strict compliance with Customer Specified Requirements (CSR) as per AS 9102. Our rigorous quality check inspections take place at every stage of the production process to ensure top-tier quality.
Once quality control (QC) is complete, we move on to the final stage of the manufacturing process: storage and packaging. We carefully store the product in the packaging room and pack all batch units for dispatch to respective clients.
At Apsis Aerocom, we are committed to leading the charge in building the technology of the future.