AS9100 D and ISO 9001:2015 certified
We are an AS9100D and ISO 9001:2015 certified company in the manufacturing industry with quality management systems to ensure that each of our projects meets the exact customer’s needs and project requirements.
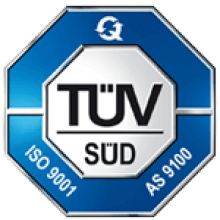
QUALITY
As a certified company, we have established robust process and workflow procedures that enable us to ensure the delivery of 100% high-quality products. Our products not only conform to the required standards but also come with complete traceability, meeting the benchmarks of world-class quality.
To ensure our products’ quality, our fully equipped quality department carries out complete validation before delivering them to our customers.
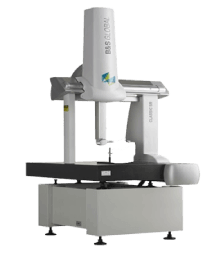
COORDINATE
MEASURING MACHINE
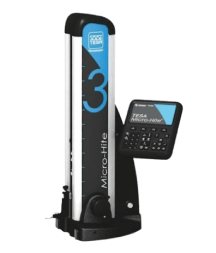
Height Gauge
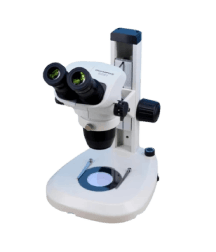
Microscope
At Apsis Aerocom, we ensure excellence through attention to detail.
Quality Assurance (QA) plays an important role in the field of precision machining & manufacturing for industries like Aerospace and Healthcare. Since 2012, Apsis Aerocom has fully implemented its quality management system to deliver high-quality and reliable services to its customers. Our strategic goal is to be a manufacturer of precision machine components of premium quality with complete accuracy.
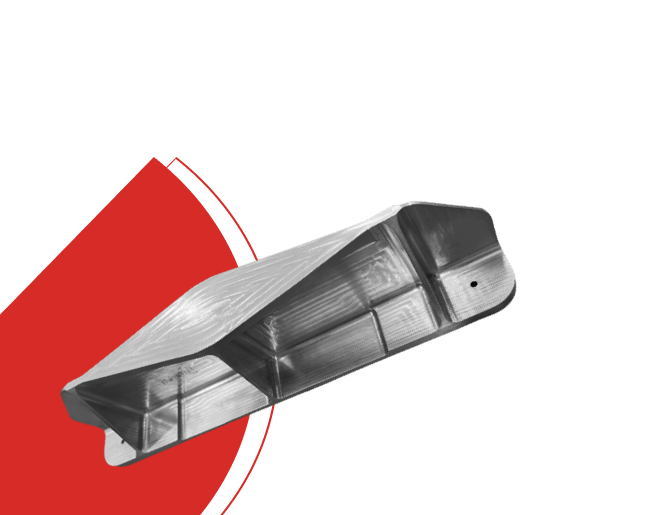
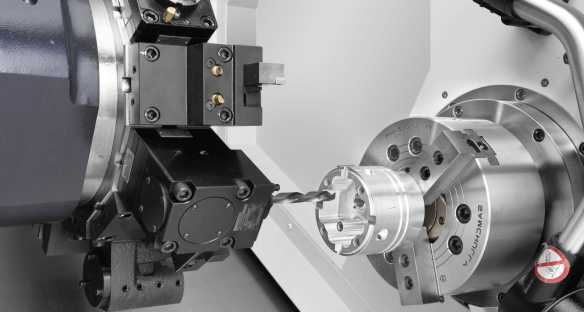
Quality Assurance includes engineers using standard measuring tools, which help them test and compare the measurement of the first sample/article to the coordinates mentioned in the documentation/CSR followed by a 100% visual test that helps in identifying the FOs (foreign objects) present in the first sample/ article.
Our holistic approach to quality covers every aspect of the company’s process in technology, including manufacturing, packaging, testing, and delivery. Apsis Aerocom’s broad focus on quality has resulted in the successful completion of numerous projects, which makes us one of the best in the manufacturing industry.
our process
quality
At APSIS AEROCOM LIMITED, we understand the critical importance of quality and precision in aerospace and healthcare manufacturing. To guarantee that every component meets the highest standards, we have implemented a meticulous inspection process that covers material incoming, in-process inspection, first article inspection (FAI), final inspection, and surface treatment.
Material Incoming Inspection: At APSIS AEROCOM, we begin the inspection process with a thorough examination of incoming materials. Our experienced inspectors meticulously inspect the raw materials, checking for compliance with the required specifications, including dimensions, composition, and mechanical properties. Any discrepancies or non-conforming materials are immediately addressed, ensuring that only high-quality materials are used in our aerospace components.
In-Process Inspection: Throughout the manufacturing process, we conduct rigorous in-process inspections to monitor and control the quality of the aerospace components. Our skilled inspectors employ various measurement tools, such as callipers, micrometres, height gauges and CMM to verify critical dimensions, tolerances, and geometric features at each manufacturing stage. This proactive approach allows us to detect and correct any deviations or potential issues promptly.
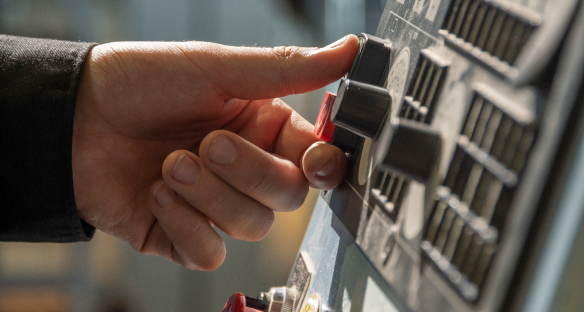
Final Inspection: Before the aerospace components are considered ready for delivery, they undergo a meticulous final inspection. Our quality assurance team employs advanced metrology equipment, including coordinate measuring machines (CMMs) and optical comparators, to verify critical dimensions, tolerances, and other specifications. Additionally, functional testing may be performed to ensure that the components meet the desired performance requirements. This final inspection guarantees that only top-quality components are delivered to our customers.
Surface Treatment Inspection: Surface treatment plays a vital role in aerospace component performance and durability. As part of our inspection process, we closely examine the treated surfaces to ensure that the required finishes, coatings, or treatments are uniformly applied and meet the specified standards. Our skilled inspectors utilise visual inspection techniques, as well as advanced surface analysis tools, to confirm the integrity and quality of the surface treatment.
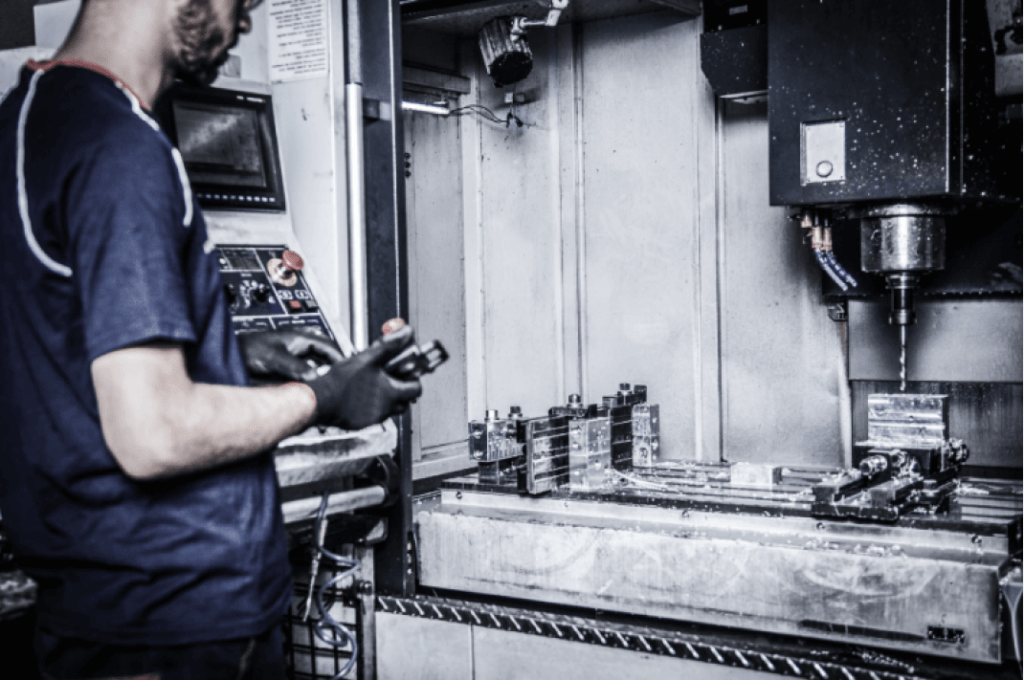
Quality Control
At Apsis, our team of dedicated Quality Heads, Engineers, and Inspectors utilize state-of-the-art machinery to compare our products against acceptance criteria and uphold exceptional quality standards. We once again conduct the First Article Inspection (FAI) in strict compliance with Customer Specified Requirements (CSR) as per AS 9102. Our rigorous quality check inspections take place at every stage of the production process to ensure top-tier quality.
Once quality control (QC) is complete, we move on to the final stage of the manufacturing process: storage and packaging. We carefully store the product in the packaging room and pack all batch units for dispatch to respective clients.
At Apsis Aerocom, we are committed to leading the charge in building the technology of the future.